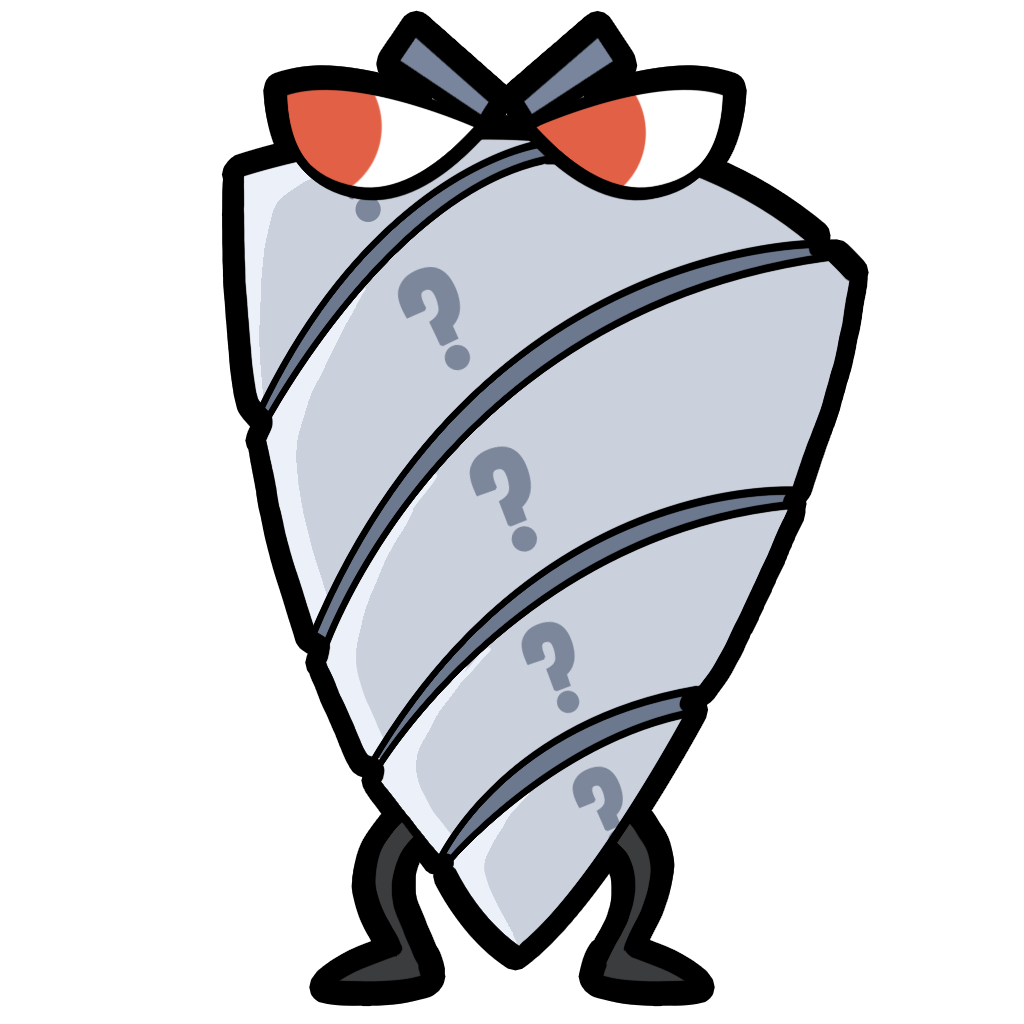
5 Whys
A problem-solving technique that involves asking "Why?" five times to drill down to the root cause of an issue.
Why Does It Exist?
The 5 Whys technique exists to simplify the process of uncovering the underlying cause of a problem. By repeatedly asking why a problem occurs, the method helps peel away the layers of symptoms to identify the base issue. It was originally developed within the manufacturing industry as part of iterative quality control processes but has since been applied across various fields for effective problem resolution.
Why Is It Important to Understand?
Understanding the 5 Whys is important because it equips individuals and teams with a straightforward and powerful approach to problem-solving. It encourages deeper inquiry and critical thinking, preventing the common pitfall of treating symptoms rather than addressing the root cause. This understanding can lead to more sustainable solutions and improvements.
How to Use It to Your Advantage
To use the 5 Whys to your advantage, apply it methodically to problems where the cause is not immediately apparent. Ensure that each answer is based on facts and evidence, and involve multiple perspectives if possible to avoid bias. This approach can help you develop more effective solutions and make informed decisions.
How It Is Used Against You
While not typically used against individuals in a manipulative sense, the misuse or superficial application of the 5 Whys can lead to incorrect conclusions. If the process is guided by bias or lacks sufficient depth, it might pinpoint incorrect root causes, resulting in ineffective solutions or further issues down the line.
Examples
A company notices a decline in product quality. Using the 5 Whys, they ask: Why is the product quality declining? The answer leads to the next question and so on, ultimately revealing that a machine on the assembly line is improperly calibrated. By identifying this root cause, the company can directly address the machine issue, preventing further quality decline and more effectively solving the problem than if they had merely increased quality inspections without understanding the true issue.